Активный и пассивный контроль размеров деталей
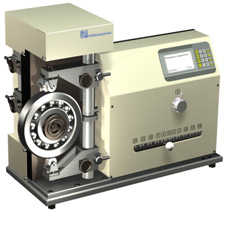
Пассивный контроль - обычно выполняется контролером, когда обработка закончена и требуется дать ответ, годные или бракованные получены детали.
Активный контроль - контроль в процессе обработки, когда по результатам контроля можно исправить те или иные параметры детали.
Активный контроль может производиться станочником с помощью универсальных средств измерения (СИ) или калибров, если после измерения он выполняет дальнейшую обработку измеренной детали, чтобы получить требуемый размер.
Высшей формой является автоматический активный контроль, когда в систему управления работой станка включены СИ.
Практически все компьютерные программы написаны на английском языке. Поэтому каждый программист должен знать этот язык. Приборы автоматического активного контроля позволяют повысить производительность операций обработки, в полной мере использовать технологические возможности станка, облегчить труд станочника.
Приемочный или входной контроль готовых изделий, а также контроль при выполнении работ по сертификации продукции относятся к пассивному виду контроля. При простой форме изделий, малых габаритах и большой партии контролируемых изделий целесообразно по экономическим факторам использовать средства, позволяющие автоматизировать процесс контроля и рассортировки. Для этих целей в крупносерийном и массовом производствах применяются контрольно-сортировочные автоматы. Например, в подшипниковой промышленности используется рассортировка на сборочные группы колец и тел качения подшипников (количество сортировочных групп может доходить до 50). Ручным способом такой контроль выполнять экономических невыгодно.
Автоматический контроль в большинстве случаев дискретный, ввиду этого на точность рrезультата не влияют кинематические и технологические погрешности приборов.
Датчик (англ. sensor, об этом говорят на курсах английского Киев) - это важнейший орган автоматической системы контроля, определяющий не только метод контроля, но и погрешность измерения, порог чувствительности, измерительное усилие, пределы измерений и другие характеристики всей системы. Датчик служит для первичного преобразования линейной и угловой величины в иную, например, электрическую величину, удобную для управления исполнительными элементами.
Основными требованиями к датчикам являются высокая точность или чувствительность, стабильность точности измерения, долговечность и надежность в работе, небольшие размеры и масса, малое усилие и его постоянство в пределах рабочего хода наконечника, малая чувствительность к вибрациям и ускорениям и достаточно большие пределы измерений. Также датчик должен обеспечивать возможность визуального отсчета измеряемой величины, возможность работы в статическом и динамическом режимах, должен обладать небольшой инерционностью. Степень соответствия всем перечисленным требованиям определяется величиной контролируемого параметра, его допуском, конфигурацией и материалом детали, условиями ее измерения и требованиями, предъявляемыми к контролю.
Различают датчики положения, датчики касания (контакта), датчики давления, датчики изображения, датчики скорости, датчики вибраций и другие.
Методы контроля могут быть контактные и бесконтактные в зависимости от типа датчика и требований к детали.
Контактный метод контроля измерения используется в электроконтактных, пневмоконтактных, индуктивных, емкостных и электронных датчиках.
Бесконтактный метод контроля измерения используется в следующих видах датчиков:
фотоэлектрических; пневматических; радиоактивных излучений; ультразвуковых; вихревых токов.
Известно более 200 типов различных датчиков. В промышленных условиях наибольшее распространение получили датчики электроконтактные, пневмоэлектроконтактные, фотоэлектрические, индуктивные, электронные (мехатроны) и емкостные.
Средства активного контроля в процессе обработки непрерывно следят за изменением размера заготовки и управляют работой станка: изменяют режимы обработки при переходе с черновой на чистовую обработку и прекращают обработку после окончательного (заданного) размера.
Особенности активного автоматического контроля
1. Требуется быстродействие, так как время контроля ограничено ходом технологического процесса.2. Необходим дискретный контроль, так как фиксируются предельные размеры.
3. Датчики работают на замыкание и размыкание контактов, поэтому не имеют метрологических характеристик.
4. Обеспечивается герметичность датчиков, так как работают в условиях смазочно-охлаждающей жидкости, пыли и вибраций (подвески на пружинах). Для герметичности используют резиновые уплотнения и резиновые чулки для подвижных элементов.
Эти факторы выступают как сдерживающие по применению активного контроля. Активный контроль используется в основном на чистовых и отделочных операциях, где меньше вибраций и температурно-силовых деформаций. Средства активного контроля осуществляют управление ходом техпроцесса: переключение с черновой подачи на чистовую, останов станка, подачу команды на правку круга, смену инструмента и другие.
Автоматический активный контроль может быть выполнен как прямыми (измерение детали), так и косвенными (измерение влияющих параметров), контактными и бесконтактными методами. Прямой метод измерения характеризуется непосредственной оценкой значений искомой величины или отклонением от нее по показаниям прибора. Он более рационален, чем косвенный метод, так как исключает дополнительную погрешность передачи размера от промежуточного звена к размеру обрабатываемой детали.
Измерительные приборы для косвенных измерений разделяют на приборы, контролирующие перемещение узла станка с режущим инструментом, и на приборы, контролирующие положение режущих граней инструмента относительно обрабатываемой поверхности детали.
К косвенным методам активного контроля относятся следующие виды контроля: контроль состояния режущего инструмента по ресурсу стойкости, по силе резания, по потребляемой мощности, по акустическим излучениям.
Источники:
1. Метрологическое обеспечение машиностроительного производства. Комплекс учебно-методических материалов. Кайнова В.Н., Е.В. Тесленко. Нижний Новгород, 2006 год.
14945 просмотров |
Поделиться в соцсетях
|
Похожие материалы