Структура управляющей программы для станков с ЧПУ
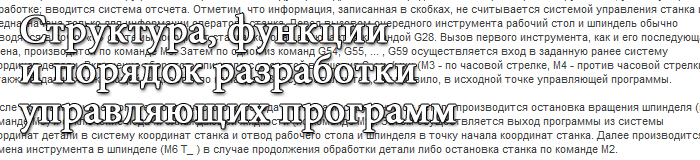
Назначение плана обработки поверхности производится на основании подразделения обрабатываемых поверхностей детали на основные и неосновные поверхности.
Основными являются точные поверхности, габаритные, формообразующие. В состав неосновных поверхностей включаются малые отверстия, малые резьбовые отверстия, лыски, пазы, канавки, фаски, остальные подобные поверхности. Основные поверхности и планы их обработки составляют базу для формирования последовательности обработки детали. Чтобы выявить весь план обработки, необходимо определить последний проход, а именно: окончательный метод и вид обработки.
Назначение окончательного метода и вида обработки выполняется по нормативным таблицам, учитывающим экономические критерии применения методов и видов обработки. Перед этим проверяется правильность задания на чертеже характеристик поверхности: точность размера, точность формы, шероховатость. Одна из этих характеристик (чаше всего — точность размера) должна быть принята в качестве основной, тgогда другие характеристики должны быть приведены в полное соответствие с ней.
Разработка управляющих программ для станков с ЧПУ производится с помощью технологических эскизов, пример которого приведен на рисунке 1.
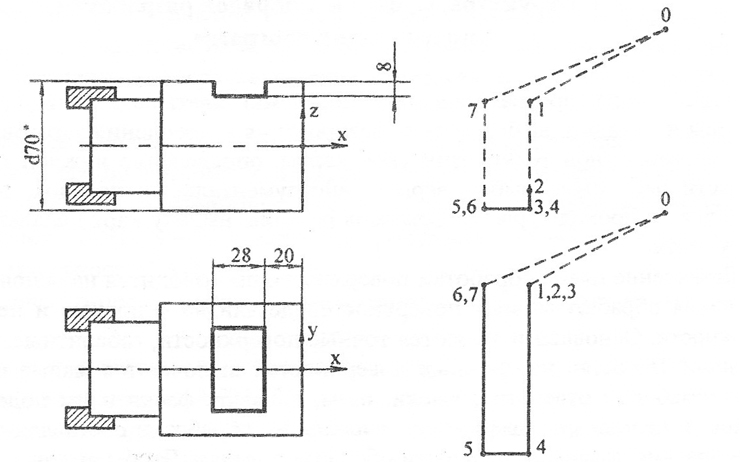
Рисунок 1. Технологический эскиз обработки детали на фрезерном станке. Таблица 1. Фрагмент управляющей программы
Отрезок циклограммы | X | Y | Z | Управляющая программа |
(0-1) (1-2) (2-3) (3-4) (4-5) (5-6) (6-7) (7-0) | -28 -28 -28 -28 -40 -40 -40 -40 | 45 45 45 -45 -45 27 85 85 | 85 37 27 27 27 27 85 85 | % o4318; (T1 end mill d20.0); (T2 face mill d80.0); G90; G28 G0 X0 Y0 Z0; M6 T1; G55; G43 X-28 Y45 Z85 H1; M8; M3 S600; Z37; G1 Z27 F100; Y-45; X-40; Y45; G0 Z85; M5 M9; G28 X0 Y0 Z0; M6 T2 (или M2); |
На эскизе представлена деталь в общем рабочем положении в конце обработки, система координат и элементы крепления. Поверхности, выполненные на данном переходе, выделяются жирными линиями; на эскизе также наносятся исполнительные размеры. Эскиз включает в себя графическое изображение траектории движения инструмента. Траектория разбивается рабочими точками на элементарные отрезки перемещения. Рабочие точки подразделяются на опорные и технологические, характеризующие соответственно изменения параметров траектории и режимов обработки. Вспомогательные перемещения рабочих органов станка, во время которых не производится непосредственно обработка, осуществляются, как правило, на ускоренной подаче. На циклограмме они обозначаются пунктирными линиями; рабочие перемещения, осуществляемые с заданной скоростью подачи инструмента, обозначаются сплошными линиями.
Структура управляющей программы
Рассмотрим структуру управляющей программы на примере циклограммы технологического эскиза (рисунок 1).В таблице 1 приведены координаты рабочих точек в конце каждого отрезка перемещений (X, Y, Z) фрезы диаметром 16 мм и соответствующий фрагмент управляющей программы.
Как видно из циклограммы, кроме рабочих перемещений фрезы, во время которых непосредственно осуществляется обработка детали, инструмент совершает следующие вспомогательные перемещения:
- движение из точки вызова и смены инструмента в шпинделе (0), координаты которой определены в системе станка, в исходную точку управляющей программы (1), координаты которой определены в системе детали; перемещение производится при одновременном включении корректора длины инструмента;
- приближение фрезы к детали и отвод от нее вдоль оси Z (точки 2,7);
- возвращение фрезы в точку вызова и смены инструмента (0) после окончания технологического перехода.
Начало управляющей программы станка с ЧПУ обозначается: «%», в следующем кадре записывается ее имя, включающее букву «о» и номер, состоящий из четырех цифр. Имя программы, например, «о4318», как правило, соответствует имени чертежно-технологического CAD/CAM файла либо номеру рабочего чертежа. В последующих кадрах обычно представлены параметры инструментов, участвующих в обработке; вводится система отсчета. Отметим, что информация, записанная в скобках, не считывается системой управления станка и предназначена только для информации оператора станка. Перед вызовом очередного инструмента рабочий стол и шпиндель обычно отводятся в точку «0» системы координат станка, которая включается командой G28. Вызов первого инструмента, как и его последующая смена, производится по команде M6. Затем по одной из команд G54, G55, ... , G59 осуществляется вход в заданную ранее систему координат детали. Включение оборотов шпинделя с частотой вращения S, мм/мин (M3 - по часовой стрелке, M4 - против часовой стрелки), а также подачи охлаждающей жидкости (по команде M8) осуществляются, как правило, в исходной точке управляющей программы.
После окончания очередного технологического перехода и отвода инструмента от детали производится остановка вращения шпинделя (по команде M5) и отключение подачи охлаждающей жидкости (по команде M9). Затем осуществляется выход программы из системы координат детали в систему координат станка и отвод рабочего стола и шпинделя в точку начала координат станка. Далее производится замена инструмента в шпинделе (M6 T_ ) в случае продолжения обработки детали либо остановка станка по команде M2.
Разработка управляющей программы для станков с ЧПУ
Технологический (изучение станков и их выбор, подбор деталей, проектирование технологического процесса); расчетно-аналитический; кодирование; запись информации на носитель; контроль, отладка и внедрение.Одной из актуальных проблем функционирования автоматизированного производства является создание комплексных САПР ТП, обеспечивающих проектирование технологических процессов для деталей всех классов в условиях мелкосерийного и серийного производства с одновременной разработкой УП для программно-управляемого оборудования. Насчитывается около 150 различных систем автоматизированного программирования. Наиболее известные и применяемые из них: ТЕХТРАН, МОДАПТ, САП-СМ4 и др.
В настоящее время находят все большее применение системы сквозного проектирования CAD-CAM-CAE («Cimatron», «UNIGRAPHICS» и др.) позволяющие осуществлять технологическую подготовку производства деталей на станках с ЧПУ без разработки документации на бумаге.
14087 просмотров |
Поделиться в соцсетях
|